Specialist Suggestions on What is Porosity in Welding and Just How to Resolve It
Specialist Suggestions on What is Porosity in Welding and Just How to Resolve It
Blog Article
The Scientific Research Behind Porosity: A Comprehensive Guide for Welders and Fabricators
Understanding the intricate systems behind porosity in welding is vital for welders and makers striving for impeccable craftsmanship. From the structure of the base materials to the ins and outs of the welding procedure itself, a plethora of variables conspire to either aggravate or alleviate the existence of porosity.
Comprehending Porosity in Welding
FIRST SENTENCE:
Evaluation of porosity in welding reveals crucial insights right into the honesty and high quality of the weld joint. Porosity, identified by the visibility of dental caries or spaces within the weld steel, is an usual worry in welding procedures. These spaces, if not effectively resolved, can jeopardize the structural integrity and mechanical residential or commercial properties of the weld, leading to possible failings in the completed product.

To find and measure porosity, non-destructive testing methods such as ultrasonic screening or X-ray evaluation are frequently employed. These strategies permit the identification of inner flaws without compromising the honesty of the weld. By examining the size, form, and distribution of porosity within a weld, welders can make informed choices to improve their welding processes and achieve sounder weld joints.
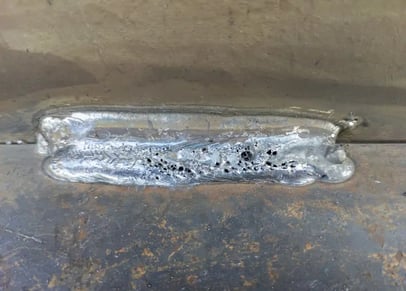
Aspects Influencing Porosity Formation
The occurrence of porosity in welding is affected by a myriad of variables, ranging from gas protecting performance to the complexities of welding specification setups. Welding parameters, including voltage, existing, take a trip speed, and electrode type, likewise influence porosity development. The welding strategy employed, such as gas metal arc welding (GMAW) or protected metal arc welding (SMAW), can affect porosity development due to variants in warmth distribution and gas protection - What is Porosity.
Results of Porosity on Weld Quality
Porosity formation substantially endangers the architectural integrity and mechanical homes of bonded joints. When porosity is existing in a weld, it develops gaps or cavities within the material, decreasing the general stamina of the next page joint. These spaces work as stress and anxiety focus points, making the weld more vulnerable to breaking and failure under tons. The existence of porosity likewise compromises the weld's resistance to corrosion, as the trapped air or gases within the voids can react with the surrounding environment, leading to degradation over time. Additionally, porosity can hinder the weld's ability to withstand pressure or influence, more threatening the total top quality and dependability of the welded structure. In crucial applications such as aerospace, automobile, or structural constructions, Recommended Site where safety and durability are paramount, the destructive results of porosity on weld high quality can have serious consequences, emphasizing the value of decreasing porosity via proper welding techniques and procedures.
Techniques to Lessen Porosity
Furthermore, making use of the appropriate welding parameters, such as the appropriate voltage, current, and travel speed, is vital in preventing porosity. Maintaining a consistent arc length and angle during welding also helps reduce the likelihood of porosity.

Using the appropriate welding strategy, such as back-stepping or utilizing a weaving movement, can also aid distribute heat equally and minimize the possibilities of porosity formation. By applying these methods, welders can efficiently reduce porosity and create high-quality bonded joints.
Advanced Solutions for Porosity Control
Applying sophisticated modern technologies and ingenious methods plays a critical role in achieving premium control over porosity in welding processes. One innovative solution is using advanced gas combinations. Protecting gases like helium or a mix of argon and hydrogen can help in reducing porosity by giving much better arc security and enhanced gas coverage. Furthermore, using sophisticated welding methods such as pulsed MIG welding or modified ambience welding can also aid mitigate porosity issues.
An additional sophisticated remedy includes using innovative welding equipment. Utilizing devices with integrated functions like waveform control and innovative power resources can enhance weld high quality and reduce porosity dangers. In addition, the application of automated welding systems with accurate control over criteria can significantly lessen porosity issues.
In addition, incorporating sophisticated surveillance and examination technologies such find more as real-time X-ray imaging or automated ultrasonic screening can assist in discovering porosity early in the welding process, permitting immediate corrective activities. On the whole, incorporating these sophisticated options can significantly improve porosity control and improve the general high quality of bonded elements.
Verdict
In verdict, understanding the scientific research behind porosity in welding is important for welders and producers to generate high-quality welds - What is Porosity. Advanced solutions for porosity control can additionally boost the welding procedure and make sure a solid and reputable weld.
Report this page